ERROR CONDITION PAPER OUT Zebra 110xi4 (4 Easy Fixes!)
There are a number of proven troubleshooting steps to follow when your Zebra 110xi4 Printer is properly loaded and you get an “ERROR CONDITION PAPER OUT” error.
Zebra 110xi4 Printer “ERROR CONDITION PAPER OUT”
When your Zebra Label Printer has the message “ERROR CONDITION PAPER OUT” on the LCD screen or on the web interface, first make sure the roll of labels is properly loaded into the printer and power cycle the printer.
Next, open the printer and ensure that nothing is blocking the sensors that detect the labels. If there isn’t anything blocking the sensor and the printer still shows the same error, perform a label calibration.
This guide is primarily for Industrial xi4 Zebra printers. If you are having this issue with any Zebra desktop label printers, please check out my post for those here.
Keep reading for more details on the above trouble shooting steps.
Zebra 110xi4 Label Printer “ERROR CONDITION PAPER OUT” – Troubleshooting
- Properly load the labels in the printer
- Power cycle the printer
- Clean off both top and bottom sensors
- Perform a label calibration
Step 1 – Properly load the labels and ribbon in the Zebra 110xi4 printer
First, ensure you have the roll of labels wound in and coming out counter clockwise and the ribbon wound out and coming out clockwise.
Feed the labels through the bumper roller up and over the media guides. This allows for a smooth pulling of the labels as it prints them out, which will maintain a straight and steady print job.
Feed the labels into the printhead and you will see the labels pop out of the snap plate, then slide it over to the firewall of the printer, tighten up your media guide and your labels are threaded.
Next, you’ll want to load the ribbon. If you’re using a brand new roll, fold over the end once you separate it from the roll, using the existing tape to secure it.
Feed the end of the ribbon roll through the bump roller right behind the printhead and above the snap plate we fed the labels under. Pull out a little excess ribbon, halfway close the printhead with the flanges open on the ribbon take-up spindle, and go under the take-up spindle and wrap around 6-7 times.
Close the print head and you have successfully loaded the labels and ribbon.
Please check out EMP Tech Groups’ video on loading labels and ribbon for a visual guide.
Step 2 – Power Cycle the Zebra 110xi4 Printer
This is often the most overlooked step in troubleshooting printers and probably in all technical troubleshooting.
Power cycling an electronic device can reset its configuration parameters or can recover from an unresponsive state of its mission critical functionality.
This action also refreshes the memory stored locally on the printer (Random Access Memory aka RAM) giving it a clean slate.
How to Power Cycle a Zebra Printer
- Turn off the printer using the switch found at the back of the printer and then unplug it.
- Wait between 15-30 seconds to allow for all the power held in the printer to dissipate.
- Plug the printer back in and turn it back on using the power switch.
If you’re printer is still showing “ERROR CONDITION PAPER OUT”, continue to step 3.
Step 3 – Clean off and align label sensors in the Zebra 110xi4 Printer
The Zebra 110xi4 label printers have two gap sensors. One sensor is on the top of the printer just below the print head. The second sensor is under where the labels come out, just before the roller.
The upper web/gap sensor is responsible for detecting the gaps between the labels. The lower web/gap and black mark sensor does the same thing, but it also senses black lines found on specific labels.
Black lines are used on labels that don’t have a gap (butt cut) or don’t have enough contrast between the liner and the labels. You can also use labels with black marks to work around a malfunctioning gap sensor.
The last sensor to clean and/or align is the media out sensor located in the upper back area of the printer. Although the previous sensors can cause a paper out error, this sensors sole responsibility is to detect whether or not labels are loaded in the printer.
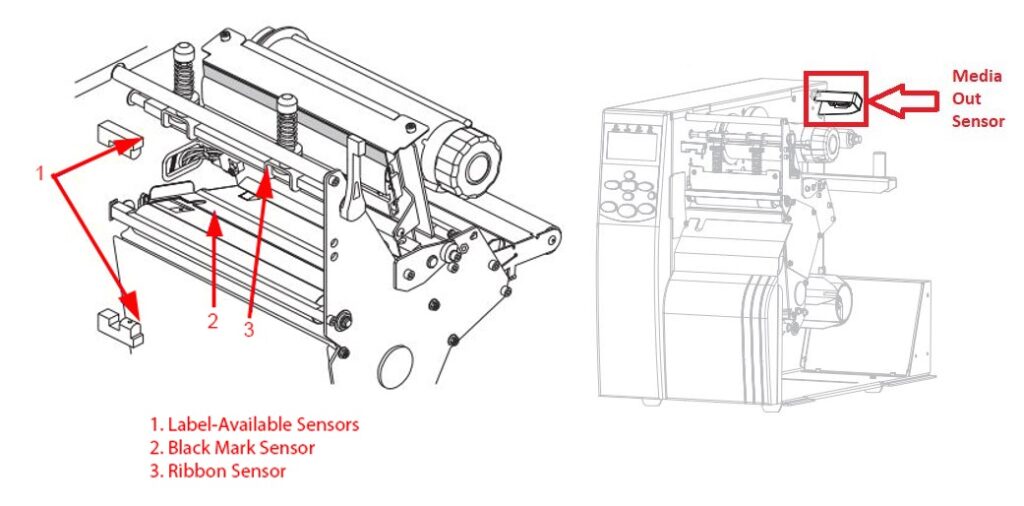
These sensors enable the printer to feed the label just far enough that you’re able to tear off the label and to prepare the next label for your next print job.
Torn pieces of labels or dirt can occasionally block these sensors leading the printer to believe there are no labels loaded in the printer.
Watch this video by “The Barcode Guy” for some more detailed instructions and visuals.
Once you remove the piece of labels and/or properly align the sensors, head to the last troubleshooting step and perform a label calibration.
Step 4 – Perform a label calibration
Calibrating the printer to the specific labels you’re using will allow the printer to accurately print on the labels as well as precisely feed the labels while printing.
First pause the printer by pressing the pause button, then hit the calibrate button to initiate the calibration process. Once the calibration is complete, you can test that this worked successfully by pressing the feed button a few times. Each time you press the button, one label should come out without any error.
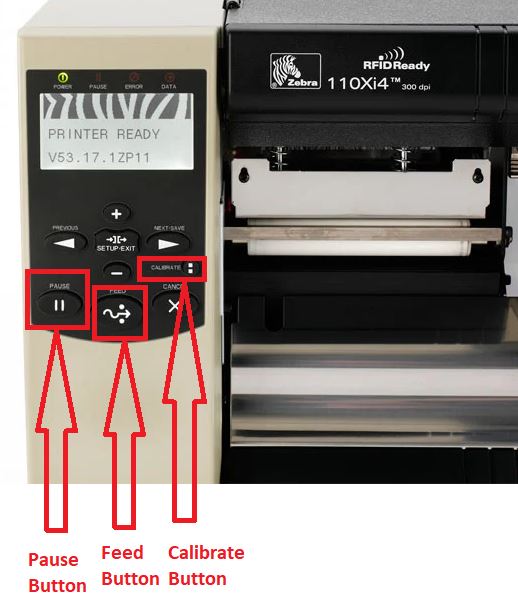
Internet enabled Zebra Printers can be set to calibrate on power up and/or when you close the head of the printer. These settings are located in the web interface, which is accessed using the printers IP address.
When you’re constantly changing label sizes, setting the printer to calibrate every time you close the printer is extremely helpful.
Conclusion
If the above steps didn’t help you solve this error, there are still a couple of steps you can take by reaching out to Zebra directly!
Before you contact Zebra, I recommend checking to see if your printer is still under warranty on Zebras Product Warranty Check page.
You can find the Serial number on the back or bottom of the label printer and enter that into their search tool. Having this serial number handy will prove useful when reaching out to the support team as well!
Contact Zebra Support:
By Phone: 1 877 ASK ZEBRA (1-877-275-9327)
By Email: https://supportcommunity.zebra.com/s/contactsupport?language=en_US
If support can’t help can’t solve this issue, you most likely have a broken or malfunctioning sensor and will have to Request a Repair.
Replacing a broken sensor yourself is possible if you have some patience. Just be aware you will void any active warranty when you open it up.
I hope you found these Zebra 110xi4 Printer troubleshooting steps helpful! If this post helped you fix the issue or if you solved it some other way, be sure to leave me a comment below so that I can include it!